Have you ever wondered how the amorphous motor core process can revolutionize electric motor efficiency?
Amorphous alloys have gained significant attention in the motor industry due to their exceptionally low-loss properties. Compared to traditional silicon steel, amorphous materials are thinner, harder, and more brittle after annealing, making their processing far more complex.
As experts in motor technology, we’ll break down the key amorphous motor core process methods used today.
Whether you’re an engineer or a tech enthusiast, join us to uncover the future of motor core manufacturing!
Characteristics of Amorphous Alloy Materials
Before diving into the techniques, let’s understand amorphous alloys. Often called “metallic glass,” these materials form when a liquid alloy rapidly cools, creating a disordered atomic structure. This unique arrangement gives them outstanding electromagnetic properties:
High permeability, low loss: Unlike traditional silicon steel, amorphous alloys have no crystalline anisotropy, leading to excellent magnetic properties. Their high resistivity and superior magnetic permeability significantly reduce energy loss during motor operation.
Corrosion resistance and toughness: Uniform structure ensures chemical stability, durability, and wear resistance.
Eco-friendly production: Simplified, energy-efficient manufacturing from material preparation to application.
However, challenges remain:
Lower saturation flux density and higher magnetostriction than silicon steel.
Sensitivity to mechanical stress during processing, leading to brittleness and lower stacking factors.
Lamination Stacking Process
For radial flux motors, the commonly used amorphous stator core processing process is shown in the figure.
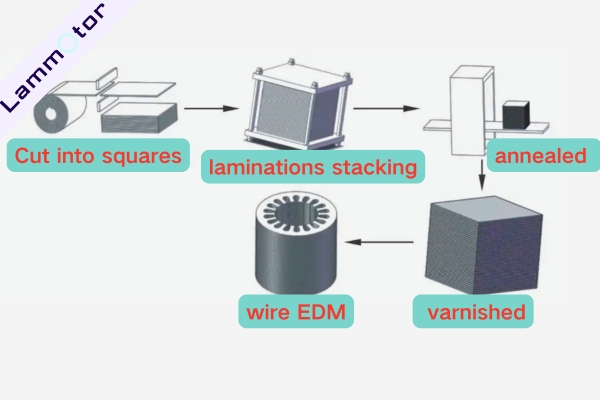
During processing, the amorphous alloy strip is first cut into a square structure and stacked into a rectangular core structure with a certain axial length.
Then the rectangular core is annealed and varnished.
Finally, the annealed and varnished core is cut. Here, we usually use wire cutting to obtain a slotted amorphous alloy core.
Since the wire EDM process is extremely time-consuming, it is difficult to meet the needs of mass core production.
To address these issues, Hitachi Research Laboratory proposed a combined processing method.
In this approach, the stator teeth and yoke are processed separately using stacking or winding techniques. These parts are then assembled using adhesives or dovetail joints, as shown in the diagram.
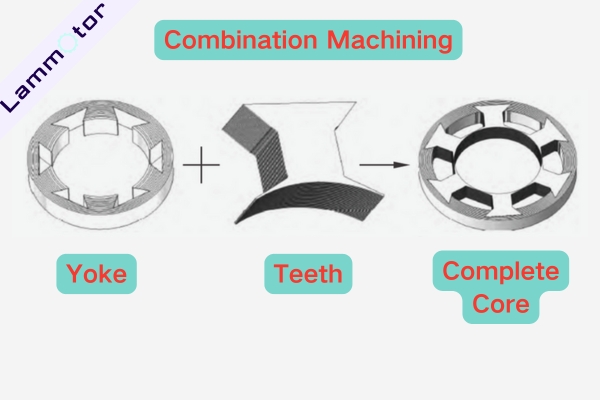
While this method saves time, it introduces additional air gaps that can affect motor performance. Moreover, the connection between the teeth and the yoke may lack structural stability.
To overcome these challenges, Toyota Central R&D Labs in Japan developed a method to form the amorphous alloy into C-shaped or U-shaped core modules.
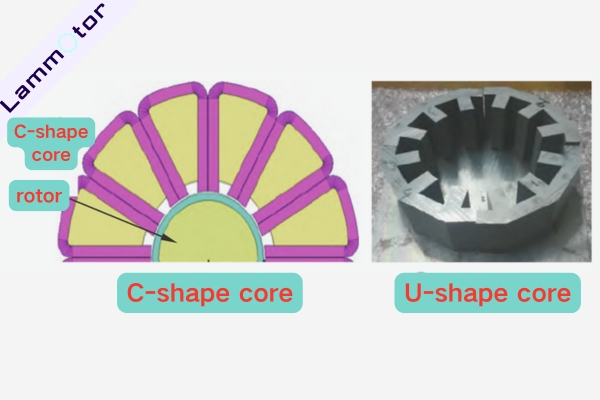
These modules are bonded together with epoxy resin to create a complete motor core, improving its structural stability. The diagram below illustrates the C-shaped and U-shaped core structures.
Rolling
The rolling amorphous core process involves continuously winding amorphous strips into a circular or rectangular shape. This method is commonly used for producing amorphous transformer cores but is also applicable to motor cores.
For axial flux motor cores, we often use winding to process.
For axial amorphous rings, we can directly use winding. As shown in the figure.
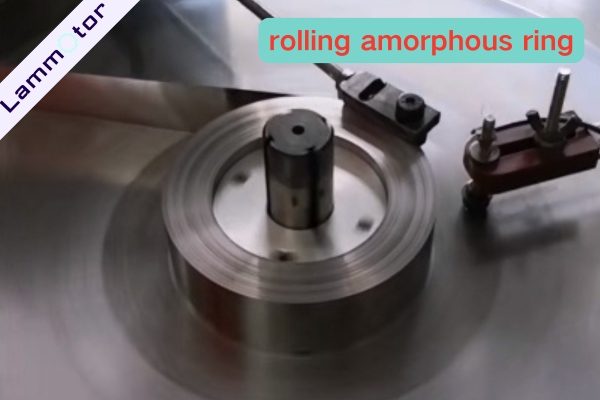
For axial flux amorphous stators, we use winding + milling.
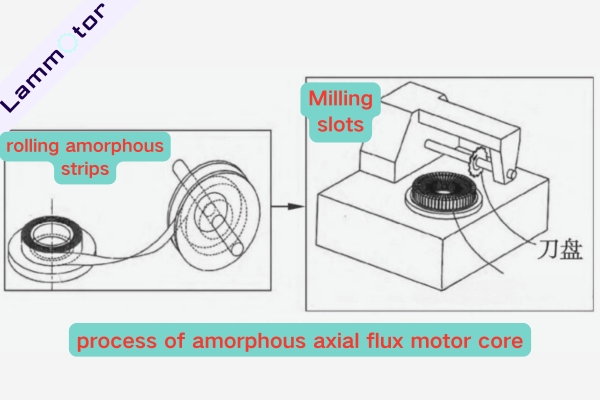
Key Steps in the Rolled Core Process:
Continuous Rolling: Amorphous strips are wound layer by layer onto a mandrel.
Shaping and Cutting: The wound core is shaped and trimmed to the desired dimensions.
Vacuum Annealing: The core is heat-treated under vacuum conditions to relieve stress and enhance magnetic performance.
Advantages:
- Reduced magnetic loss due to continuous structure.
- Less mechanical stress on the material during processing.
Alternative slotting methods include dual-blade cutting with bottom drilling or abrasive waterjet machining. While faster, these introduce stress that degrades magnetic performance.
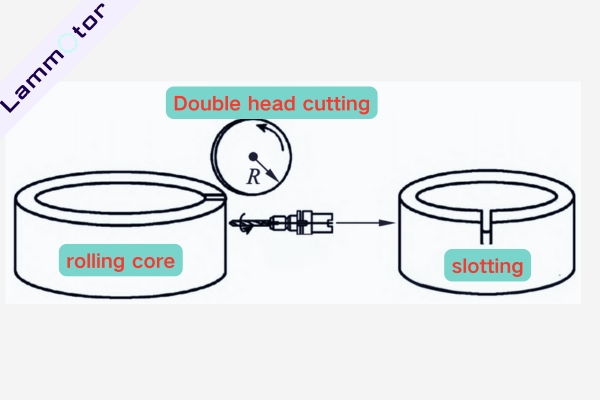
While these processing methods can reduce core manufacturing time, they also introduce mechanical stress during machining, which can negatively affect the core’s magnetic performance.
Hitachi Research Laboratory proposed a process where amorphous alloy strips are wound to form stator core modules. These modules are then bonded together using epoxy resin to create a complete core, as shown in the diagram.
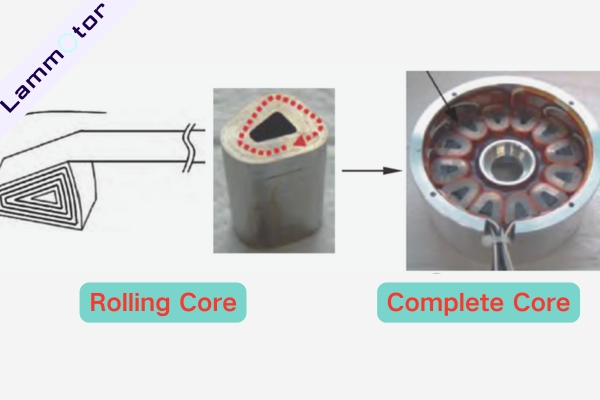
This method is particularly suitable for single-stator, dual-rotor motor structures, as it effectively avoids the instability caused by connecting the stator teeth and yoke. To further reduce stress between the core modules.
Stamping
Stamping, a staple for silicon steel cores, is tough for amorphous alloys. Yet Chinese firms like Qingdao Yunlu Advanced Materials have made breakthroughs. Their amorphous motor core process includes:
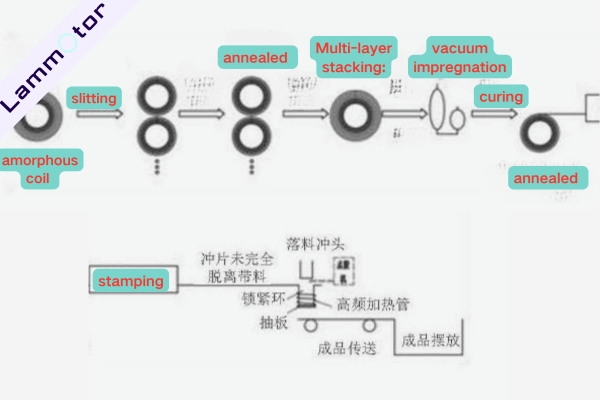
- Material prep: Flattening ribbons to remove stress.
- Slitting & heat treatment: Stabilizing the material.
- Multi-layer stacking: Compensating for ultra-thin ribbons (0.025mm vs. silicon steel’s 0.35mm).
- Vacuum impregnation & drying: Enhancing layer adhesion.
- Progressive stamping: High-speed, precision shaping with durable molds.
Challenges in Stamping:
- Brittle material prone to cracking.
- Rapid mold wear and high costs.
- Precision alignment for multi-layer stacks.
- Stress sensitivity impacts magnetic performance.
Challenges in Processing Amorphous Alloy Strips
From a mechanical perspective:
Amorphous strips are hard, with high requirements for alignment accuracy, precision, and processing stability, making them difficult to machine.
High Hardness:
Amorphous strips are thin, hard, and almost non-ductile, with a Vickers hardness of approximately 900, comparable to tungsten carbide and five times that of silicon steel.
Annealing Process:
The purpose of annealing is to reduce internal stress and restore magnetic properties. However, annealing makes amorphous alloys brittle, increasing the difficulty of subsequent processing, lowering the yield rate, and reducing product consistency and stability. Additionally, during motor assembly, fragile amorphous cores are prone to generating fragments, which can severely affect motor performance.
Precision Requirements:
Amorphous strips are approximately 0.025 mm thick, compared to 0.35 mm for silicon steel sheets, requiring higher precision in stacking, alignment, and overall processing stability.
From a magnetic perspective:
Low Magnetic Induction:
Amorphous alloys have lower magnetic induction and weaker magnetic permeability. This puts them at a disadvantage in high-torque output applications. Compared to silicon steel, amorphous alloys require improved magnetic induction to prevent magnetic circuit saturation.
High Magnetostriction Coefficient:
The magnetostriction coefficient of amorphous strips is several times larger than that of silicon steel and is highly sensitive to mechanical stress.
To maintain magnetic performance, the clamping force during core stacking should not be too high. This results in a lower lamination factor, making amorphous cores looser than silicon steel cores, which can lead to higher motor vibration and noise.
When the rotor surface of a high-speed motor is tightened using carbon fiber or non-magnetic alloy sleeves with a certain preloading force, it can also alter the magnetic properties of the amorphous material.
Conclusion
Choosing the right amorphous motor core process is crucial for optimizing performance and efficiency in electric motors. Each process—stamping, rolling, and lamination stacking—offers unique benefits tailored to different manufacturing needs.
Did you know? Our company specializes in manufacturing high-performance amorphous stator cores tailored to your needs. Whether you’re optimizing for low loss, durability, or compact design, we’ve got you covered. Contact us today to discuss how amorphous alloys can elevate your motor projects!